Tank sealing is an underlying cog in the wheel of diverse industries, including petrochemicals, water treatment, food processing, transportation, and many more. It is instrumental in ensuring the tanks’ reliability, halting leakages, maintaining the material integrity of stored substances, and averting potential hazards.
Sealing of tanks refers to the process of using specialized sealants to prevent stored contents from escaping, thus maintaining the integrity of the tank. which involves an intricate series of steps such as surface preparation, selecting appropriate sealants based on the tank and its contents, applying said sealants, and post-application inspections.
This comprehensive guide aims to delve into the world of tank sealing, providing a resourceful, helpful and intuitive manual for ensuring the safe and efficient sealing of tanks.
Types of Tanks and their Sealing Requirements
In order to understand the process of tank sealing, it’s crucial to first recognize the varied types of tanks and their unique sealing necessities. Broadly, tanks are classified according to their usage as storage and fuel tanks, transportation tanks, and chemical and water tanks.
Storage tanks are typically large structures used to store liquids like oil, gas, and water. These tanks are often subjected to stringent sealing requirements due to the nature and volume of the contents. Transportation tanks, such as those used in trucks or ships, require sealants that can withstand constant movement and varying temperatures.

On the other hand, chemical tanks that store aggressive or corrosive substances call for seals and sealants with excellent chemical resistance.
Different sealing materials and techniques are necessary depending on the type and function of the tank. For example, a welded steel tank storing petroleum may require an epoxy or polyurethane-based sealant to effectively seal the tank, while a water tank may need a more flexible, hydro-resistant sealant.
As we tread further into this guide, it’s important to know that sealing requirements are not one-size-fits-all but differ as per the tank type, the substance stored, and environmental factors among other variables.
WAGNER Automotive Tank Sealing Kit
WAGNER Automotive Tank Sealing Kit offers a complete solution for the long-term coating of sheet metal, plastic and aluminium tanks.
shop nowSurface Preparation for Tank Sealing
One cannot stress enough the importance of robust surface preparation before applying any sealant to a tank. An immaculate, debris-free tank surface not only ensures better adhesion of the sealant but also amplifies the seal’s longevity and effectiveness.
Cleaning is the primary step towards surface preparation. Here, techniques such as chemical cleaning, pressure washing, or steam cleaning can be employed based on the extent of contamination present. While chemical cleaning helps eliminate stubborn residues, pressure washing or steam cleaning provides an aggregated effect of removal and disinfection.
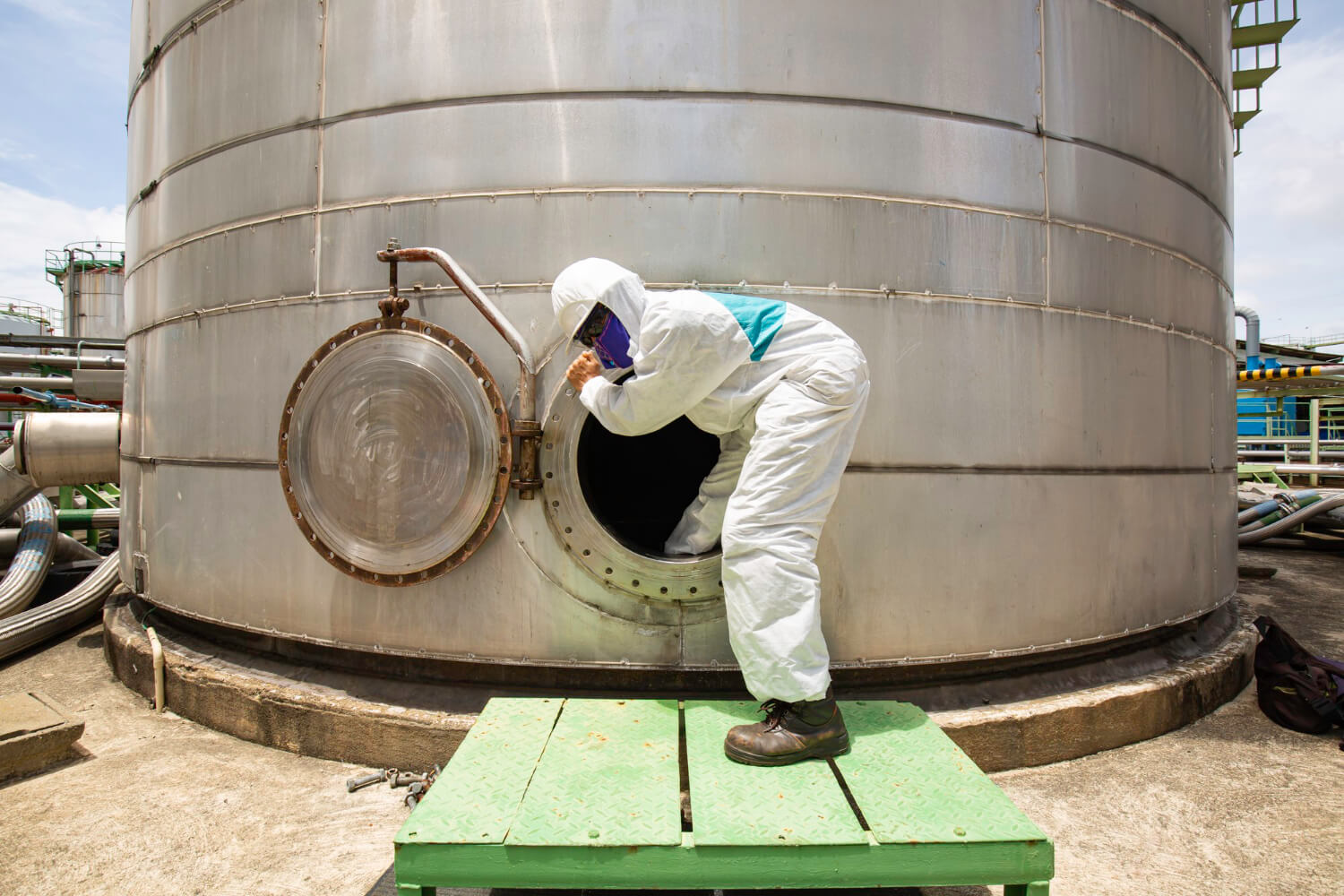
Post-cleaning, a detailed inspection is mandatory to identify potential problem areas like cracks, corrosion or peeling paint that may pose obstacles to the sealing process. These areas need immediate attention using suitable repair methods.
For metal tanks, welding is an efficient technique to seal off any rust or cracks. For non-metallic tanks, repair materials such as bonding agents or restorative coatings can be used. Remember, meticulous surface preparation is the foundation stone for safe and efficient tank sealing.
Choosing the Right Sealant
The success of a tank sealing process heavily depends on the choice of sealant. When deciding on a sealant, it is paramount to consider the gas tank sealer‘s material, the amount reproduction gas tank‘s contents, and the prevailing environmental conditions. Each of these factors has a major impact on how well a selected sealant will work and for how long.
For instance, if you are working with a tank made of metal like steel or aluminium and it is meant to store petrochemicals, epoxy or polyurethane sealants can be an excellent choice. These sealants are robust and resistant to chemicals, making them well-suited for heavy-duty applications.

If, however, the tank is dedicated to storing potable water, then a non-toxic sealant is necessary to ensure that the water in gas tanks remains safe for consumption.
Environmental factors like temperature and humidity also have a bearing on the sealant’s performance. Certain sealants may not function optimally under extreme climates. Therefore, understanding the local environmental conditions where the tank operates is critical.
Meanwhile, in emergencies, there are quick-sealing options available that can provide temporary relief until a permanent solution is found. The mantra to remember is that the right sealant is contextual and needs careful deliberation based on specific requirements.
WAGNER Tank Sealing Resin
WAGNER Tank Sealer will seal small leaks (seams, welds, pinholes). Multiple applications can be applied and excess resin can be used for further applications.
shop nowSealing Techniques and Best Practices
Understanding numerous sealing techniques and adhering to best practices ensure an efficient sealing process. While techniques like caulking, adhesive bonding, and joint sealing are standard, the selection depends on the nature and size of holes in the area to be sealed.
The nature of the task will also determine whether a spray, roller, or brush is apt for sealant application. Brushes are perfect for smaller tanks or intricate areas, whereas rollers and sprays are more efficient for larger surfaces.

It is good practice to ensure the tank surface is dry and free from any contaminants prior to application. Attention to environmental factors such as temperature and humidity is also vital because variances can affect the sealant’s performance. If multiple coats are necessary for optimum protection, each layer should be completely dried before the next is applied.
Furthermore, strict adherence to the manufacturer’s instructions regarding the correct mixing and application of sealants is essential to achieve a foolproof seal.
Inspecting and Testing the Sealed Tanks
Successfully sealing a tank isn’t the endpoint of the task; it’s just another step towards the new tank and ensuring its safety and efficiency. The sealed tank should then go through rigorous inspections and testing.
Commencing with a visual inspection is wise. Check the application for uniformity in thickness and smoothness, and search for any gaps or bubbles that might mar the top sealer‘s effectiveness. Should these be found, address them immediately to prevent future problems.
Thereafter, the tank should be subjected to leak testing methods to guarantee it’s secure and leak-free. Various testing methods can be employed, such as pressure testing, vacuum testing, or hydrostatic testing, depending on the type of tank in question and the available testing resources. This thorough inspection and testing regimen ensures maximum sealing efficiency and guarantees the tank’s long-term serviceability.
Lube-Shuttle®: Pistol Grip Grease Gun
The Best Pistol Grip Grease Gun You Have Yet to Try No mess, no waste, no headaches. Lubricate tools and machinery with this grease gun.
shop nowMaintenance and Monitoring
Keeping tanks functioning optimally and ensuring the longevity of their seals requires consistent maintenance and monitoring. Regular inspections, ideally conducted by trained professionals, are crucial. This involves a thorough check of the tanks’ physical structures, the condition of their sealants, filters and other features critical to their integrity and performance.
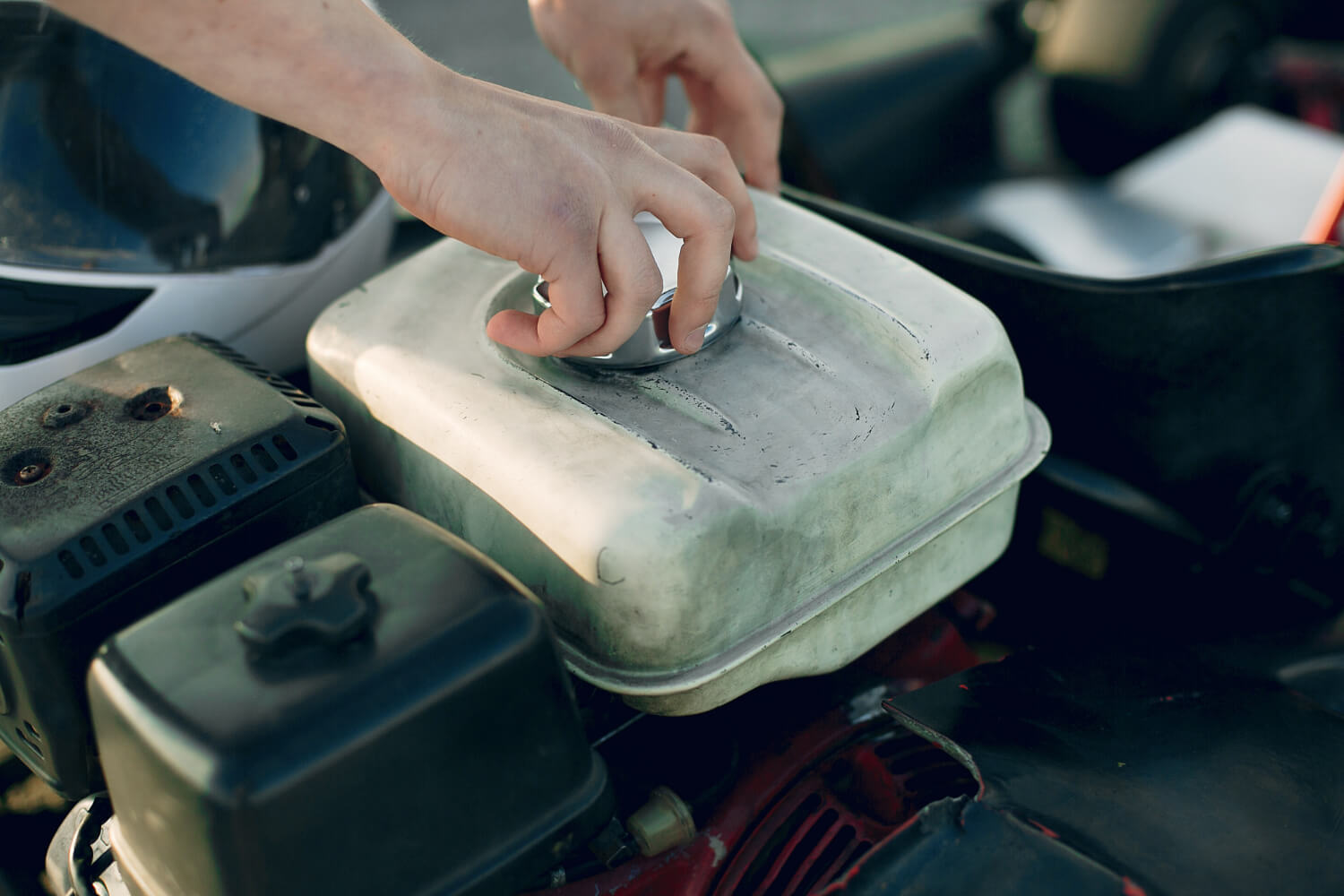
Periodic cleaning and maintenance come next. This isn’t just about keeping the tanks clean; it’s about preemptively identifying potential issues. A slight crack or a small leak might not seem significant in the short term, but, if left unchecked, can turn into a major headache, not to mention the potential losses in contents and revenue. Regular maintenance is about nipping such potential problems in the bud.
While many aspects of maintenance can be preventive, it is also essential to have procedures in place for on-time repairs. As soon as an issue is spotted, immediate action should be taken to fix it. This might mean applying a fresh layer of sealant or, in more serious cases, replacing the whole gas tank.
Safety Precautions while Sealing Tanks
Sealing tanks, while a routine process for many industries, isn’t without its hazards. The use of Personal Protective Equipment (PPE) is vital in this context. Tank sealing personnel should always wear safety glasses, gloves, masks, and coveralls to protect themselves from potential injuries and chemical exposures.
Equally critical is maintaining a safe and well-ventilated working environment. In many cases, the sealants employed can give off potentially harmful fumes. Therefore, ensuring adequate airflow during the sealing process helps mitigate health risks and enhances the efficiency of the process.
The presence of flammable vapours and materials makes no smoking and open flame rules essential. It’s crucial to avoid anything that could potentially spark a fire or result in an explosion, thus ensuring a safer environment for all involved in the sealing process.
AirTec Grease: Li400 Extreme Duty Grease
Li400 is the flagship grease from AirTec. Thickened with Lithium complex and reinforced with AirTec/Wagner Micro Ceramic Li400’s performance under extreme temperatures and pressures puts it in a class of its own.
shop nowConclusion
The importance of safe and efficient tank sealing cannot be overstated. Beyond safeguarding the valuable or sensitive contents stored in tanks, proper sealing, and maintenance procedures ensure environmental safety, extending the service life of tanks and preserving resources.
By following the guidelines and best practices discussed, you contribute to a safer, more efficient, and environmentally friendly industrial landscape. Regular maintenance, safety precautions, and the right choice of sealant are key to a successful tank sealing process and prolong the gas tank sealer‘s life.
FAQs
What is the best way to seal a water tank?
The best way to put gas tank sealer kit a water tank involves choosing the right non-toxic sealant that suits the tank’s material, ensuring the tank is clean and dry before application gas tank sealant, applying the sealant as per manufacturer’s instructions, and letting it cure for the recommended time.
What material is used for tank seals?
Different kinds of sealants can be used for fuel tank sealer, including but not limited to, epoxy, polyurethane, silicone, and butyl rubber sealants. The choice of sealant depends on factors like the fuel tank sealer‘s material, its contents, and the external environmental conditions.
Which waterproofing is best for an underground water tank?
A waterproofing method involving a combination of a liquid rubber membrane and a waterproof cementitious coating is generally considered best for underground water tanks. This not only provides a waterproof seal but also strengthens the tank structure.
What is a sealing tank?
A sealing tank or a gas tank liner, in the context of this guide, refers to a storage tank (like a water tank or fuel tank) where a sealant has been applied to prevent leaks and contamination, thus protecting the tank’s contents and increasing its service life.
How do you seal water damage?
Sealing water damage involves properly drying and cleaning the affected area, applying a stain-blocking primer to prevent the water stain from showing through, and then applying a sealing product that can effectively block water.